Biomimetic fiber composite
ICDITKE, University of Stuttgart
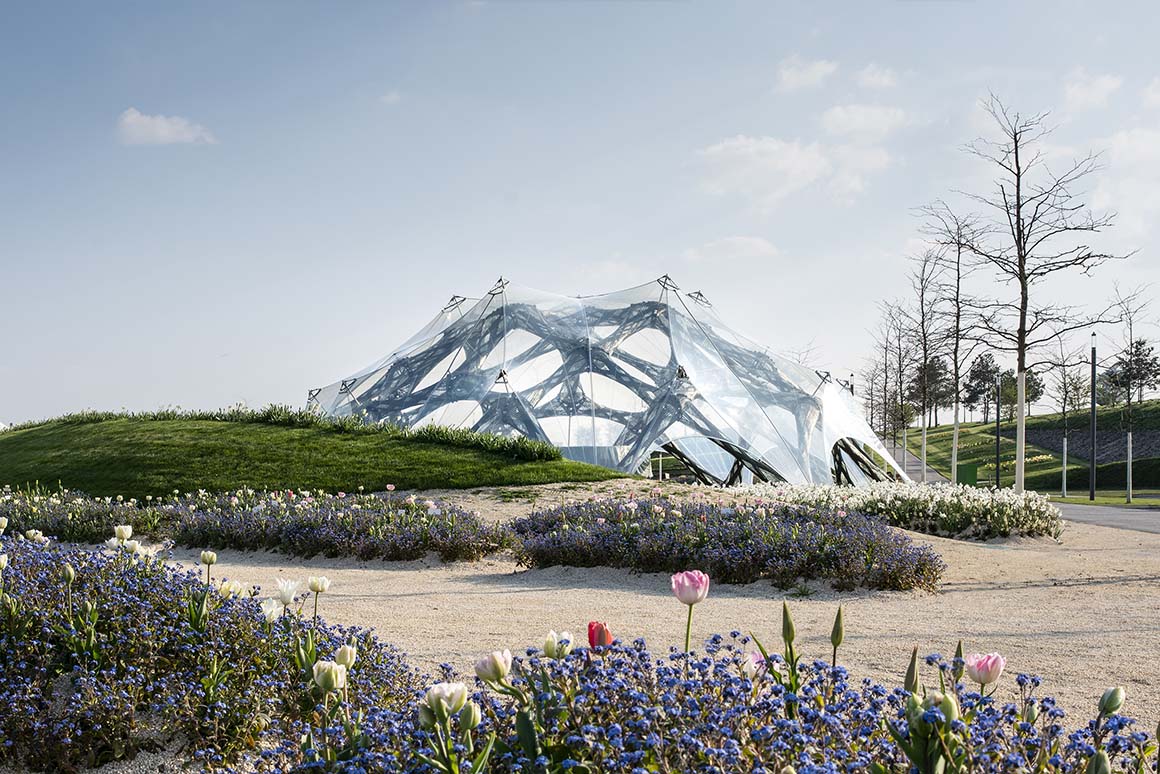
Embedded in the landscape of the Bundesgartenschau (Germany’s biennial horticultural show), the BUGA Fiber Pavilion offers visitors a futuristic architectural experience, after years of biomimetic research at the University of Stuttgart.
The pavilion demonstrates how combining cutting-edge computational technologies, with construction principles found in nature, enables truly novel and genuinely digital building systems. The pavilion’s structure is robotically produced from advanced fiber composites, not only highly effective and exceptionally lightweight, but also providing a distinctive yet authentic architectural expression in an extraordinary spatial experience.
In biology, most load-bearing structures are fiber composites, such as cellulose, chitin or collagen, and a matrix material that supports them and maintains their relative position. The performance and resource-efficiency of biological structures stems from these fibrous systems. Their organization, directionality and density is finely tuned and locally varied in order to ensure that material is only placed where it is needed.
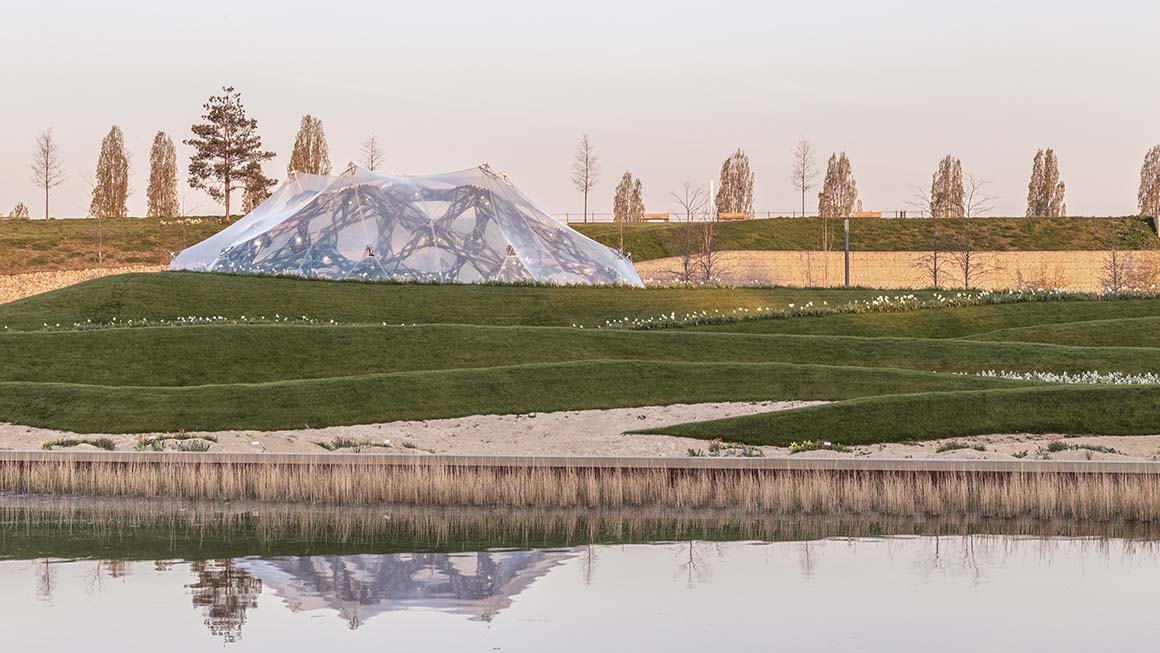
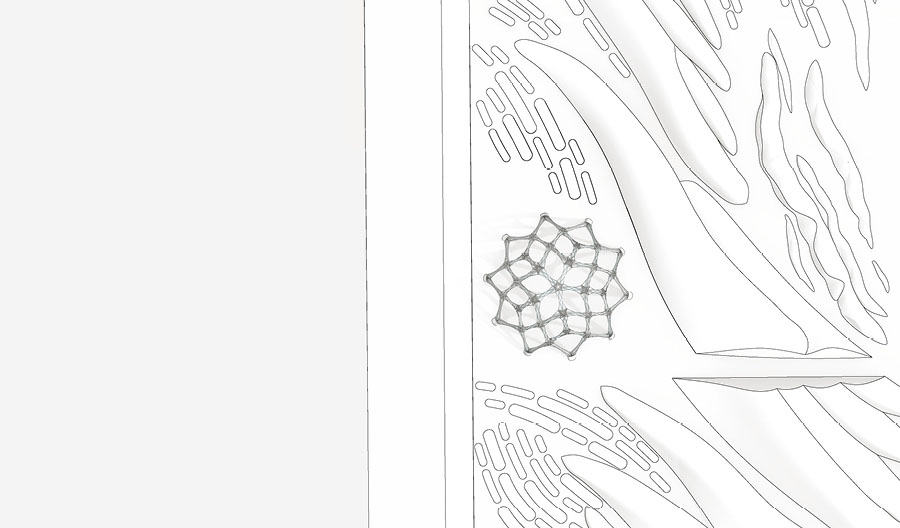
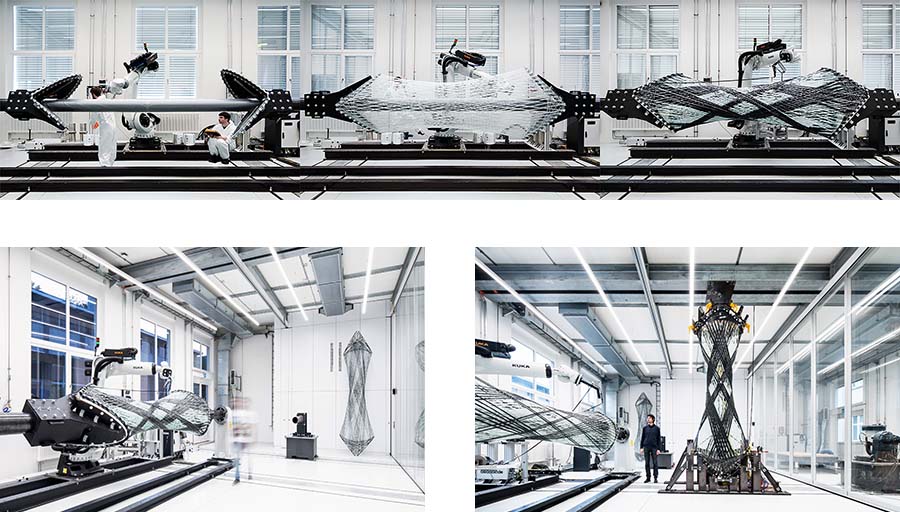
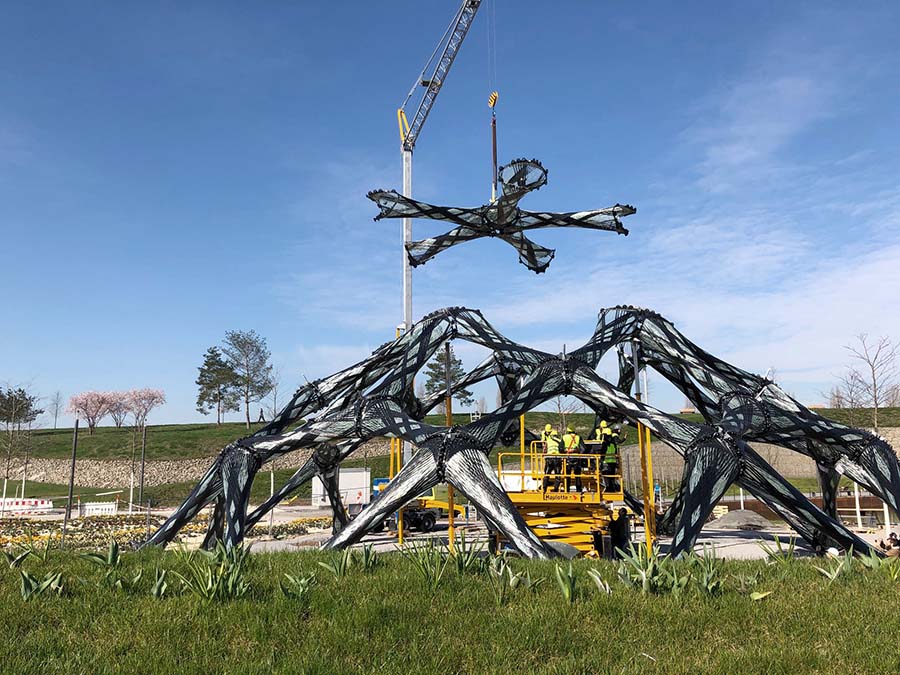
The BUGA Fiber Pavilion aims to transfer this biological principle into architecture. Manmade composites, such as glass- or carbon-fiber-reinforced plastics, are ideally suited for such an approach, because they share fundamental characteristics with natural composites.
The pavilion is made from more than 150km glass and carbon fibers. It required a novel co-design approach, where architectural design, structural engineering and robotic fabrication work in continuous computational feedback. The fiber arrangement, density and orientation of each building component was calibrated, structurally tuned and architecturally articulated, while remaining directly producible.
The building components’ manufacturing approach was pioneered at the University of Stuttgart: fibrous filaments are robotically placed between two rotating winding scaffolds. The predefined shape of the building component emerges from the interaction of the filaments, eliminating the need for any mould or core. This allows for bespoke forms for each component, without any economic disadvantage, and with no production waste or material off-cuts. During manufacturing, carbon fibers are placed on a lattice of translucent glass fibers where they are structurally needed, resulting in distinctive looking, highly load-adapted, components.
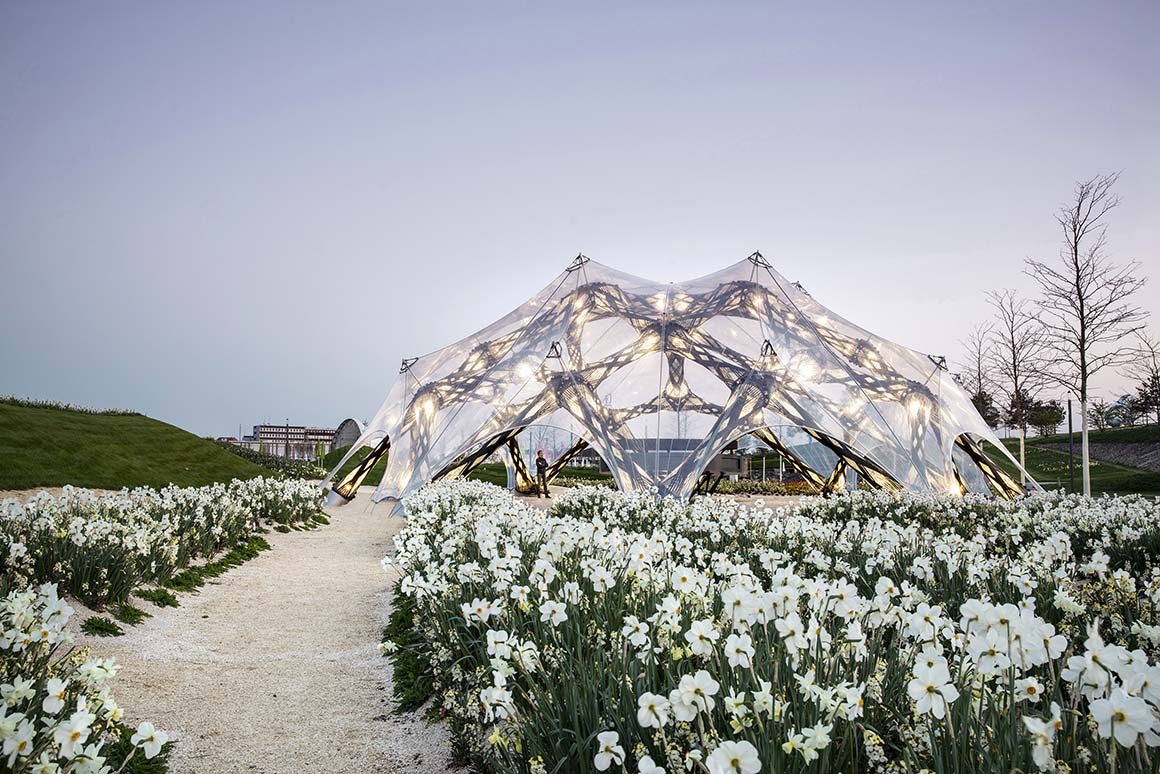
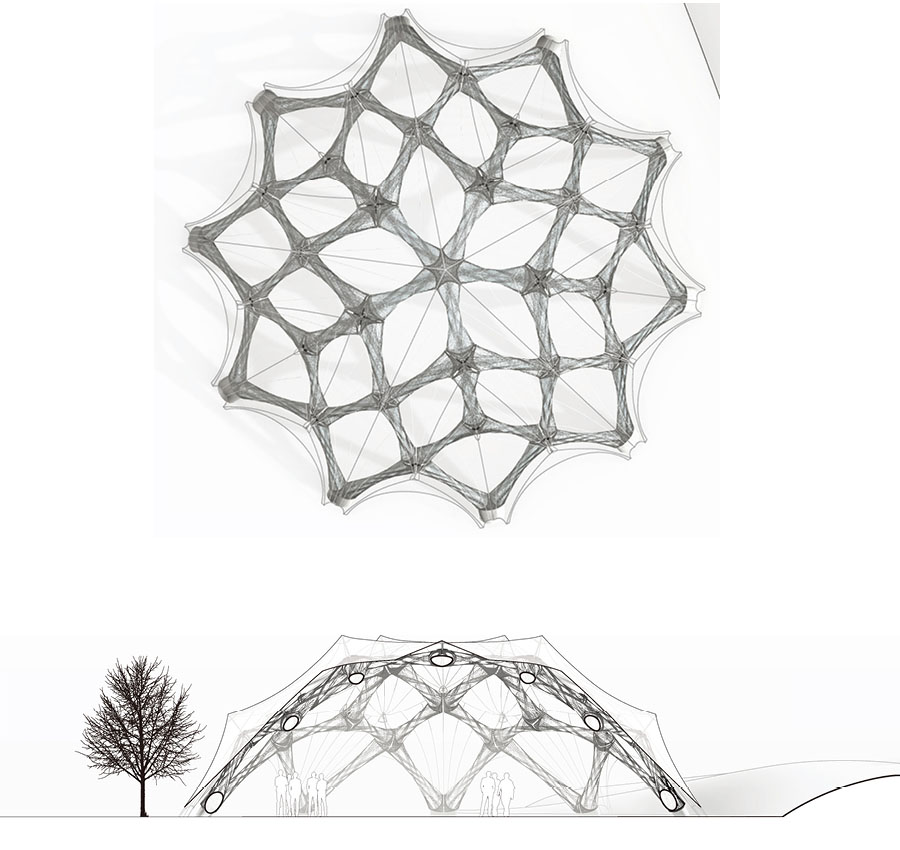
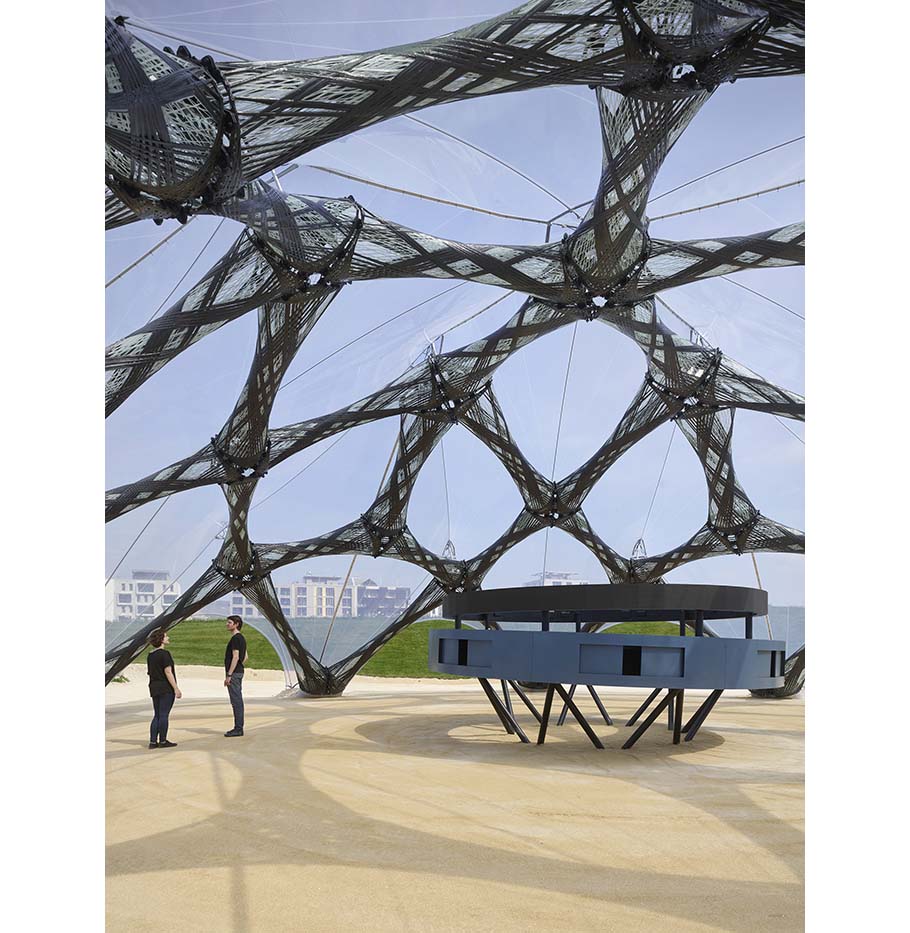
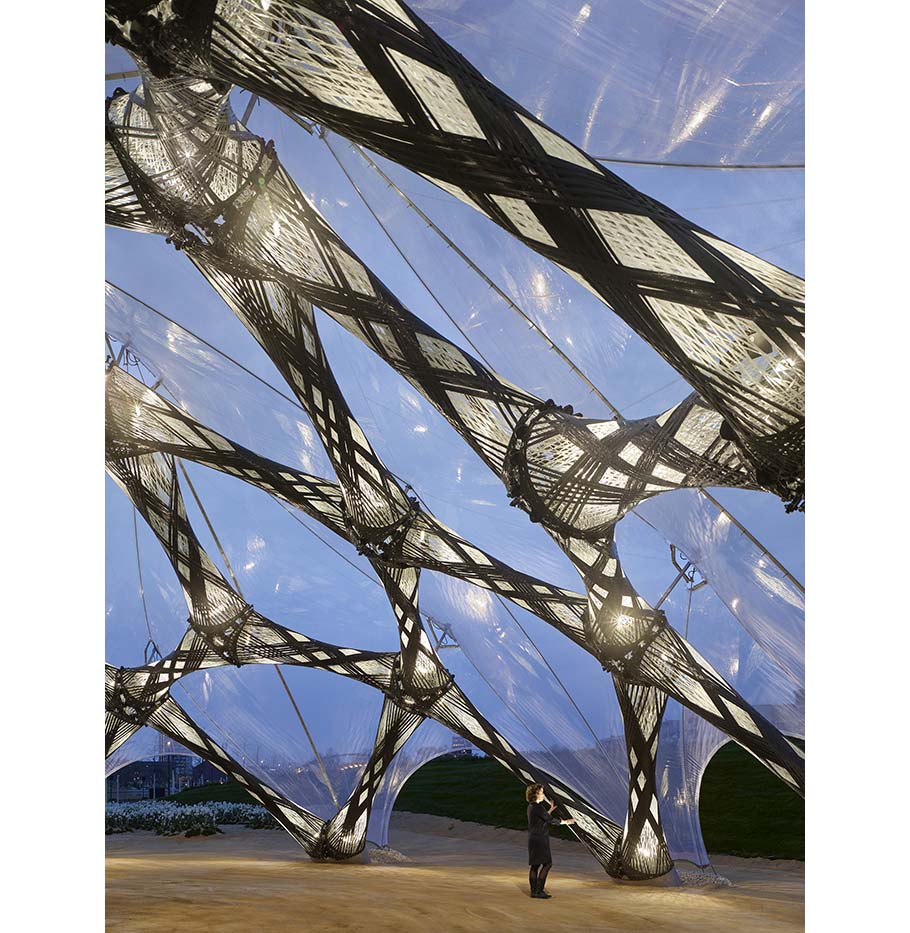
The pavilion, covering an area of 400 square meters, is enclosed by fully transparent, mechanically pre-stressed ETFE membrane. The primary load-bearing structure is made from 60 bespoke fiber-composite components. At 7.6kg per square meter it is approximately five times lighter than a steel structure.
The pavilion translates technical innovation into a unique architectural experience. The black carbon filament bundles, wrapping around the translucent glass fiber lattice like flexed muscles, create a stark textural contrast, intensified by the gradient from sparse carbon filaments at the top towards a denser application on the slenderest components at the bottom.
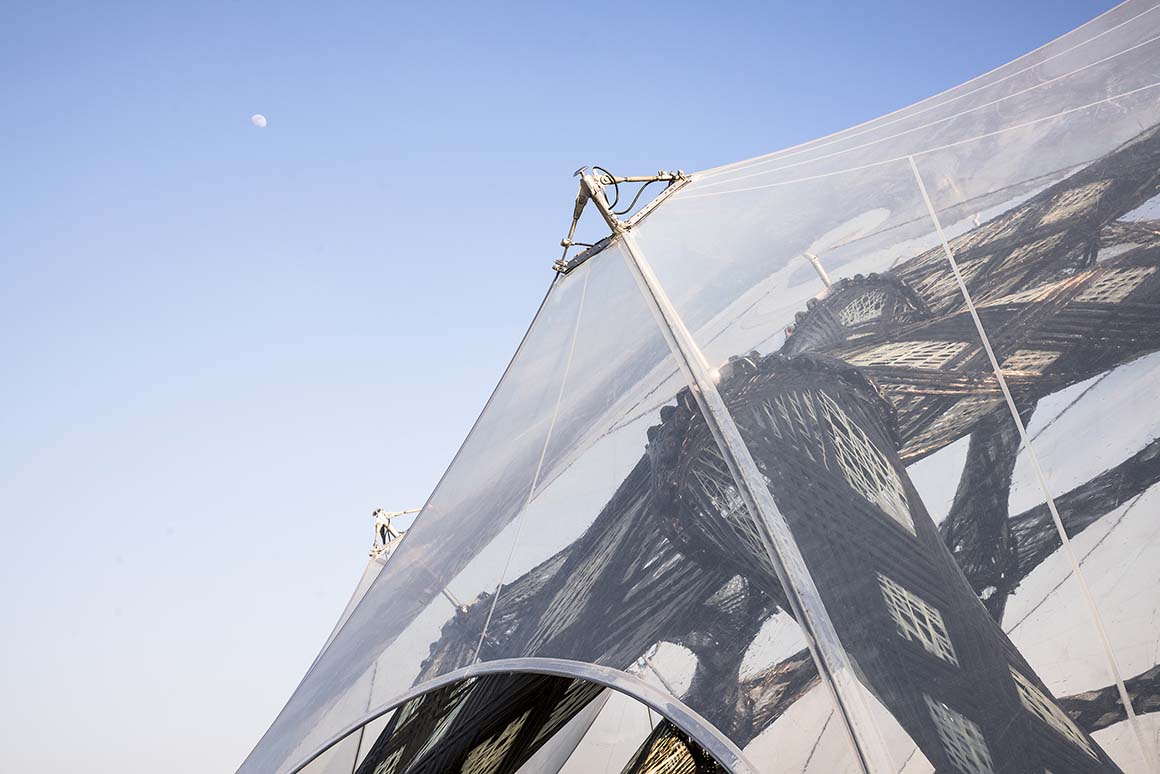
Project: BUGA Fibre Pavilion / Project partners: ICD-Institute for Computational Design and Construction, University of Stuttgart_Prof. Achim Menges, Serban Bodea, Niccolo Dambrosio, Monika Göbel, Christoph Zechmeister; ITKE–Institute of Building Structures and Structural Design, University of Stuttgart_Prof. Jan Knippers, Valentin Koslowski, Marta Gil Pérez, Bas Rongen; FibR GmbH, Stuttgart_Moritz Dörstelmann, Ondrej Kyjanek, Philipp Essers, Philipp Gülke; Bundesgartenschau Heilbronn 2019 GmbH_Hanspeter Faas, Oliver Toellner / Project building permit process: Landesstelle für Bautechnik_Dr. Stefan Brendler, Dipl.-Ing. Steffen Schneider; Proof engineer_Dipl.-Ing. Achim Bechert, Dipl.-Ing. Florian Roos; DITF German Institutes of Textile and Fiber Research_Prof. Dr.-Ing. Götz T. Gresser, Pascal Mindermann / Project funding: Land Baden-Württemberg, Universität Stuttgart, Baden-Württemberg Stiftung / GETTYLAB, Forschungsinitiative Zukunft Bau, Pfeifer GmbH, Ewo GmbH, Fischer Group / Dimensions: 23m diameter / Covered area: 400m2 / Weight of loadbearing fibre composite structure: 7,6kg/m2 / Construction system: 60 load bearing robotically fabricated glass and carbon fibre composite elements, out of 150.000m glass and carbon fibres; transparent, mechanically pre-stressed ETFE membrane / Completion: 2019 / Photograph: ©BUGA; ©ICD_ITKE; ©Roland Halbe (courtesy of the architect)